Materiaalwetenschap en -techniek
Onze materiaalkundigen zijn gespecialiseerd in het evalueren van systemen en componenten vanuit een materiaalperspectief. Met hun uitgebreide kennis van materiaalontwerp en -productie en van storingsanalyse en -testen kunnen onze experts de hoofdoorzaak van materiaalprestaties en storingsproblemen vaststellen.
Wanneer componenten of systemen niet meer werken zoals bedoeld, omdat er iets kapot is gegaan, gelekt, vervormd, gecorrodeerd, geërodeerd, enzovoort, is het de taak van de consultant om de hoofdoorzaak van het defect vast te stellen.
Rimkus adviseurs op het gebied van materiaalwetenschap en engineering maken gebruik van alle beschikbare middelen en analytische hulpmiddelen om niet alleen te bepalen wat er is gebeurd en hoe herhaling kan worden voorkomen, maar we kunnen ook de verantwoordelijke partijen identificeren voor de toewijzing van schade. Ons team heeft jarenlange ervaring met storingsanalyse en corrosie-evaluaties in een breed scala van industrieën en soorten systemen die nodig zijn om de klus te klaren.
Rimkus heeft ook een toegewijd team van deskundigen die gespecialiseerd zijn in een breed scala aan materiaaltesten, analyses en laboratoriumdiensten. Bezoek onze pagina Materiaaltesten en onderzoek voor meer informatie.
Onze diensten voor materiaalwetenschap en engineering
Iron-based materials still constitute most of the metals used in the world today. Due to their high strength, versatility, and low cost, steel, and iron products are all around us. Rimkus has extensive experience and testing capabilities of ferrous metals, assisting clients in various industries such as construction, oil and gas, automotive, machinery, and commercial and residential buildings.
From structural component failure in the building, pressure vessel explosions, broken drive axles, and crane failures, to water leaks in pipes and hoses, Rimkus experts can perform metallurgical testing, determine the cause of the failure, assist the client in materials selection, and propose the proper remediation.
Corrosion poses the biggest challenge to ferrous metals. Corrosion damage often results in damage to the properties and environment, loss of equipment, business delay, and even personal injuries. Rimkus experts can investigate the type and origin of the corrosion, determine if the incident was caused by other factors, and provide prevention/control methods.
2 Case studies
1. Pinhole leak on a welded steel water pipe
Background: Pinhole leak occurred on the steel pipe in a recently installed cooling water system. The leak caused substantial concerns about the sustainability of the system.
Services Provided: Rimkus was retained to determine the cause of the leak and evaluate the integrity of the rest of the pipe system. Several issues relating to corrosion, manufacturing, and operations were discovered during our investigation. We performed the following analysis.
- Conducted an on-site joint inspection of the pipe system.
- Reviewed applicable codes and standards, and other expert reports.
- Performed metallurgical tests and determined the cause of the incident.
- Evaluated the condition of the system based on the materials test results.
- Proposed recommendations for replacement and operation.
2. Dredging barge failure
Background: A dredging barge sank during the operation at a job site. The steel pontoons were damaged, and the barge turned over resulting in the total loss of the equipment on the barge. It was later retrieved and disassembled for investigation.
Services Provided: Rimkus was retained to examine the barge and investigate the origin and cause of the incident. During our investigation and analysis, Rimkus examined the morphology of the fracture, the sequence of the incident, and the condition of the barge.
Rimkus concluded:
- The dredge sank due to the impact damage to the pontoon.
- Several welds cracked and failed due to the overload during the barge’s capsizing or retrieval process, instead of manufacturing defects.
- The balance and loading condition of the barge, and the corrosion and general condition of the steel pontoon were evaluated and determined not to be contributing factors to the incident.
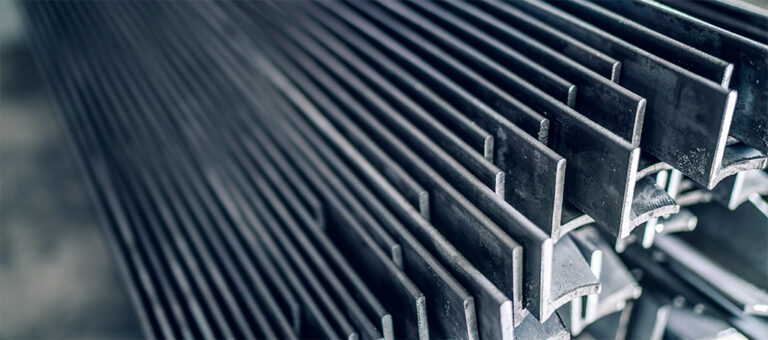
Metal products not produced from iron are an ever-increasing segment of the materials world. Copper (and copper alloys) and aluminum have been stalwart companions of iron-based alloys for centuries and are used both structurally, decoratively, and for their unique properties such as conductivity, low density, and corrosion resistance.
Other non-ferrous metals like nickel-based superalloys, cobalt alloys, zinc alloys, titanium alloys, and magnesium alloys have been developed for special markets and niche uses.
The materials experts at Rimkus have extensive experience with a broad range of systems containing non-ferrous metals and how those metals perform in specific environments. With extensive experience, the Rimkus team can work with any non-ferrous metal in any environment, such as:
- Copper tubing and brass fittings in potable water systems
- Copper tubing in HVAC (Heating Ventilating and Air Conditioning) systems
- Structural aluminum components in multiple applications
- Aluminum alloy bicycle components
- Die-cast zinc plumbing fittings and components
- Titanium biomedical implants
- Titanium-headed hammers
- Cobalt alloyed gate valves
- Magnesium housing assemblies
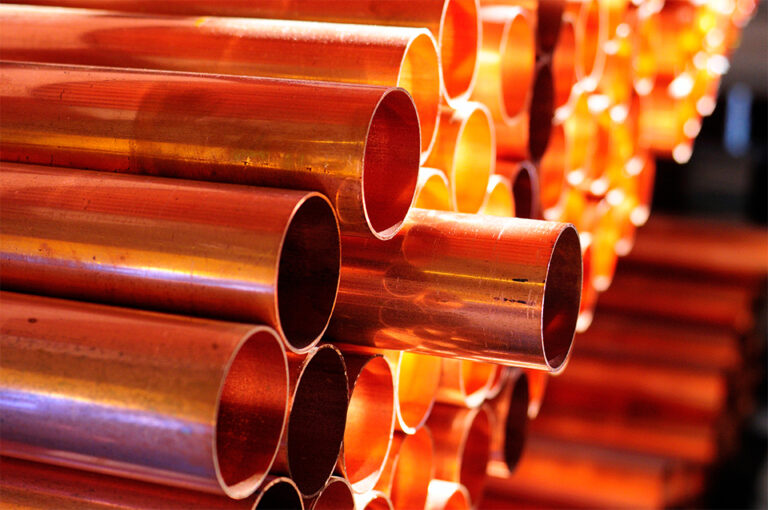
Polymers/plastics are encountered every day in our automobiles, households, buildings, electronics, textiles, adhesives, packaging, paints, coatings, etc.
When you are faced with a polymeric material issue, turn to Rimkus’ expertise for identifying the root cause and origin of the failure, characterizing critical properties, or determining interactions between the polymer and other substances.
By carefully investigating polymeric failure mechanisms, Rimkus experts can identify stress overloads, environmental and chemical degradation, manufacturing (molding) issues, improper service conditions, or misuse. Depending on the situation, our experts may search for voids, blisters, molding defects, contamination, absorbed solvents, oxidation, weathering, poor adhesion, mechanical failure, discoloration, and brittle or ductile fracture.
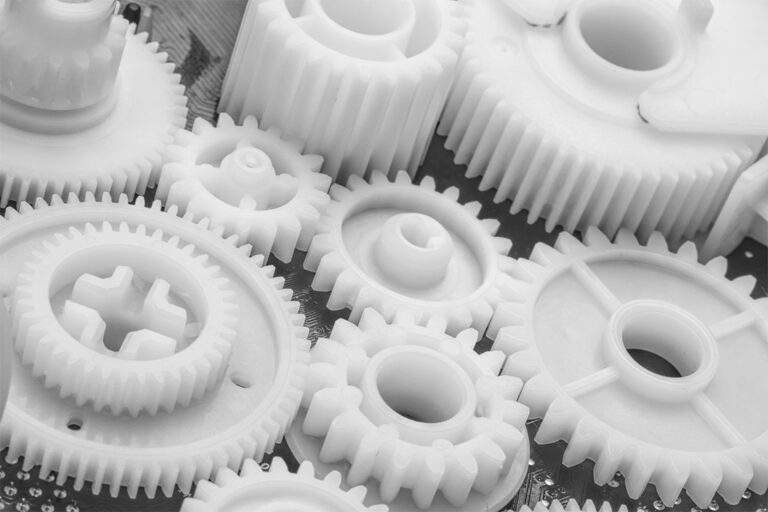
Ceramics and glasses are often the best, or only, material choice for an application. Their combination of high strength, temperature resistance, surface hardness, and transparency-by-design make their use more prevalent than one might expect.
Rimkus uses optimum methods to identify modes of failure or characterize these materials for their composition and physical properties. With specialized expertise in window glass and e-glass, we can identify the source and origin of scratches, discoloration, or permanent chemical etching.
Rimkus has the analytical competence to measure outgassing, binder loss, or absorbed fluids in ceramics and glass. We offer imaging of fracture surfaces, stains, and surface chemistry; cross-sectioning to evaluate cracks, voids, and intergranular phases; characterization of thin layer coatings; identification of organic contaminants absorbed during service; and measurement of decomposition due to oxygen, fluorine, and chlorine.
2 Case studies
1. Permanently etched window glass
Background: Shortly after a cleaning service had power washed the siding of a house with large, customized windows, the window glass was found to be opaque in patterns that resembled splashing. Cleaning the windows did not offer any improvement.
Services Provided: Rimkus was retained to examine the windows and determine if there was permanent damage and how extensive the damage to the windows was in terms of cost. Rimkus inspected approximately 25 customized windows on the inside and outside surfaces in accordance with ASTM (American Society for Testing and Materials) standards.
Several were permanently etched by chemicals. A survey was completed that identified how many windows would have to be replaced. Acetate replicas from the windows were taken to identify the depth of the damage and to pull off chemical residues for analysis.
Rimkus concluded:
- The same chemicals used by the cleaning company were identified in the residues taken from the windows.
- If the cleaning company had thoroughly rinsed the windows on the same day that they power washed the house siding, there would not have been damage to the glass. It was a week later that the windows were rinsed. By then the windows were permanently etched.
- Less than half the windows had enough damage to require replacement.
2. Explosive fracturing of engineered stone bathtub
Background: An elderly woman was filling a recently installed bathtub, fabricated from engineered stone. She was in the kitchen when she heard what she thought was an explosion. When she entered the bathroom, the bathtub had a large fracture, from top to bottom, and water had flooded the floor.
Services Provided: Rimkus was retained to examine the bathtub and determine the cause and origin of the fracture. We used a flexible scope to inspect behind and underneath the bathtub around the fracture. A square section was removed using a circular saw to allow for a flexible hose from the back. The fracture initiated at the corner of the square.
Rimkus concluded:
- Engineered stone is under a high degree of residual stress because of the manufacturing process. Stone powder is mixed with a polymer and poured into a mold. As the polymer cures and shrinks, stress develops.
- The plumber had disregarded the installation instructions that emphasized, under no circumstances, should the engineered stone be cut or drilled.
- The plumber’s saw cut created a stress concentration at the sharp corner of the square. As the bathtub was filling with hot water, the high residual stress at the sharp cut released, forming a crack that rapidly propagated across the tub, sounding like an explosion.
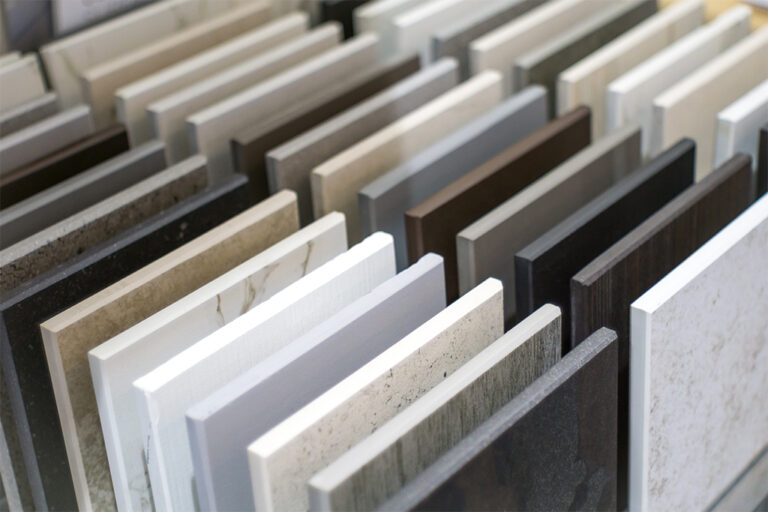
Composites materials are becoming a larger and larger part of our lives from sports equipment to boats; they can be found everywhere. Rimkus experts can help wherever reinforcing agents (glass and carbon and wood fibers) are added to a matrix such as polymers and rubber to produce composite materials.
Our investigative experts with the help of our laboratory can identify manufacturing defects: delamination/porosity, poor wetting of the reinforcement by the resin, errors in layup orientation, or simply inappropriate material selection. Field abuse, user errors, and damage beyond normal use can also be investigated by our experts.
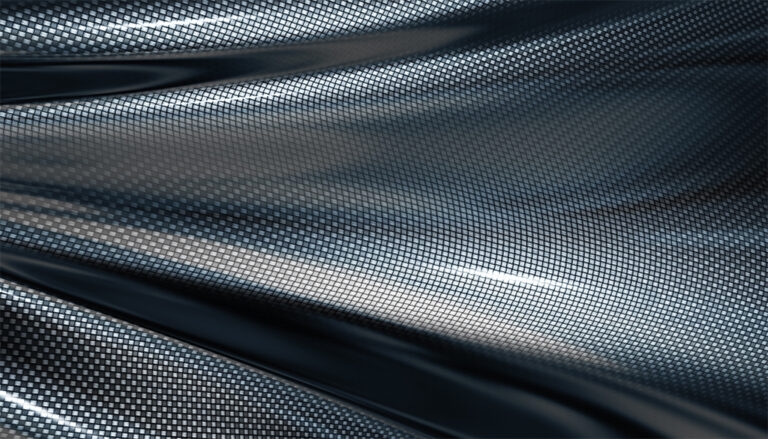
Moderne gebouwen zijn meer dan alleen hout en bakstenen en bevatten complexe materialen in hun constructie. Rimkus deskundigen kunnen antwoorden geven op veel vragen over hoe bepaalde bouwmaterialen functioneerden, presteerden of degradeerden. In samenwerking met onze vastgoed- en werktuigbouwkundige, elektrische en sanitair (MEP) praktijken kan Rimkus complexe zaken onderzoeken waarbij bouwmaterialen betrokken zijn van traditionele bouwmaterialen zoals hout, beton, baksteen en mortel tot technische oplossingen waarbij meerlaagse constructie met polymere membranen, metalen en zelfs composietmaterialen betrokken zijn.
Examples of projects which Rimkus can help with include for example identifying the root cause of discoloration of roofing, siding, pool liners, bricks, and pavers. Failure analysis of concrete and mortars can be performed with the help of our laboratory facilities. Drywall, plaster, mortars, and other cementitious compounds as well as various composite decking materials have also been analyzed by our Rimkus experts and we can help analyze raw materials contamination which can result in widespread field failures.
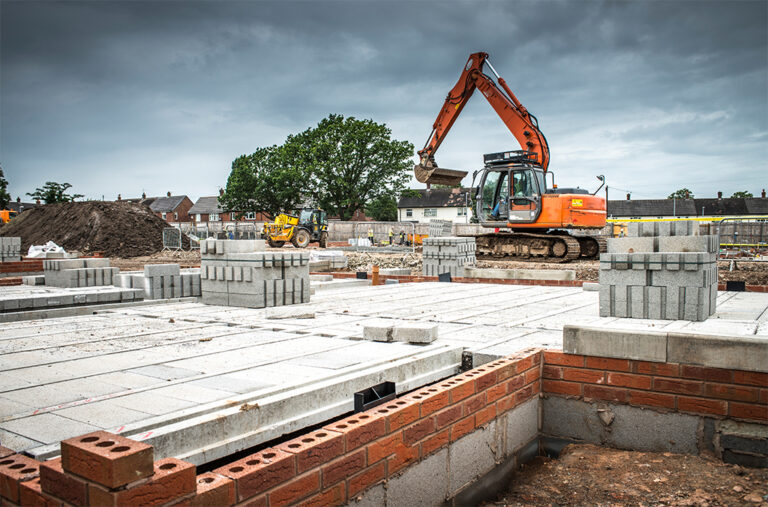