

Failure Analysis of Ruptured Inergen Fire Suppression Cylinder
December 22, 2023
Background
A ruptured cylinder from a fire suppression system was received by the Rimkus Materials Testing and Investigation team for analysis to determine the cause of failure. The cylinder was filled with an INERGEN (52% nitrogen, 40% argon, and 8% carbon dioxide) mixture at approximately 2300 psi at the time of rupture event.
Services Provided
Rimkus experts performed a series of testing and analytical techniques on the ruptured cylinder to provide a full failure analysis report to the client. These tests and services included the following:
- Visual, stereoscopic, and scanning electron microscope (SEM) examinations
- Elemental analysis (EDS)
- Metallography (microstructure evaluation)
- Chemical composition (OES)
- Tensile testing and hardness
Results indicate the rupture initiated at a longitudinal alignment of several pre-existing axial cracks on the cylinder’s interior. The pre-existing cracks were characterized by black oxide-covered, arc-shaped crack fronts initiating from the interior surface and penetrating approximately 50% – 80% through the cylinder wall. The presence of black oxide indicates the cracks have been present for a long period of time and may have occurred at a high temperature during manufacturing thermal processing. Black oxide may also be a result of corrosion along the pre-existing cracks in a low oxygen environment.
There was evidence of two stages of crack progression before the rupture; however, the time between the stages could not be determined. Black oxide and significant corrosion along the crack lengths were exhibited in both regions. The second stage of crack progression appeared to have been either very old or occurred over a long period of time.
The black oxide on the pre-crack surfaces indicates the cracks have been present for a long period of time and may have occurred at high temperature during manufacturing thermal processing. Black oxide may also be a result of corrosion along the pre-existing cracks in a low oxygen environment.
Numerous long-term, pre-existing axial cracks were similarly noted near the rupture site. The observed pre-existing internal cracks were limited to within approximately 18 inches (0.5 meters) of the tank bottom. Shallow, pre-existing circumferential cracks were observed on the circumferential fracture surface along the tank bottom. These were a continuation of the axial rupture at the bottom of the cylinder (see Figure 1). There appeared to have been active corrosion along the pre-existing cracks. The remainder of the fracture surface (beyond the pre-existing crack zones) exhibited features indicative of rapid ductile overload.
Other than the pre-existing cracks, no other unusual conditions were found in the cylinder microstructure. The cylinder material meets the Department of Transportation 178.37 Specification 3AA and 3AAX seamless steel cylinders for chemical composition. The cylinder steel exhibited a yield strength of 74,700 psi and an ultimate tensile strength of 105,100 psi.
Photos
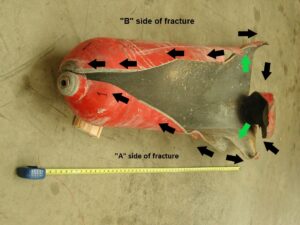
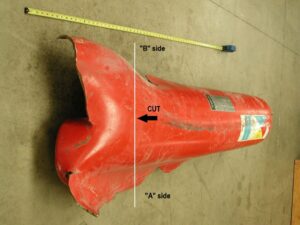
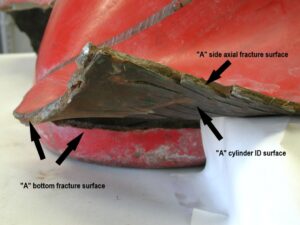
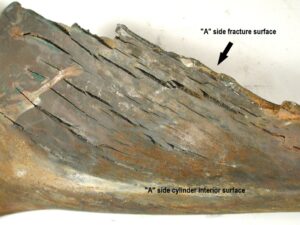
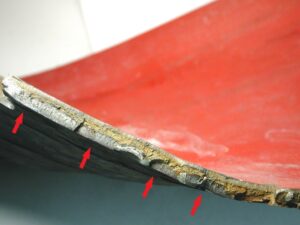
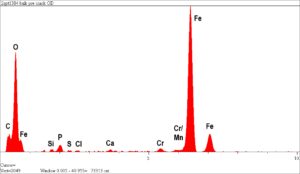
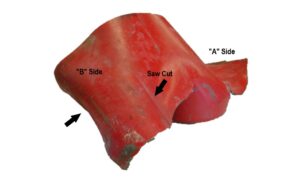
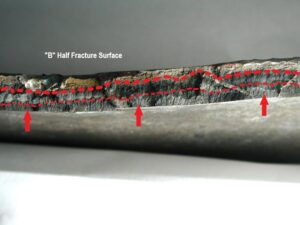
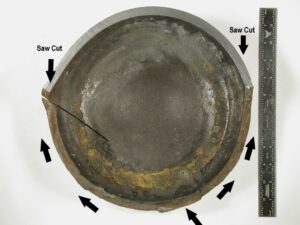
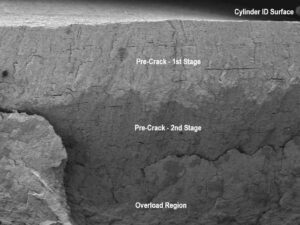
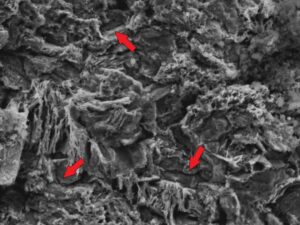
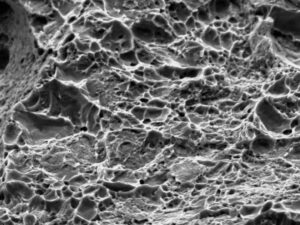

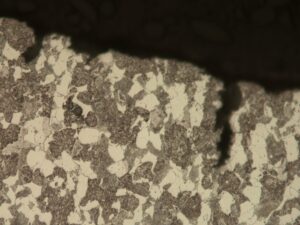
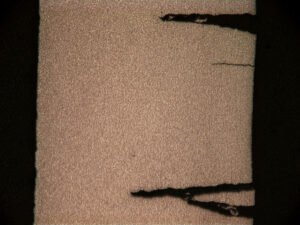
Sorry, no posts matched your criteria.